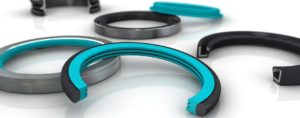
It’s no secret that seals play a critical role in ensuring proper function of rotary systems, but designers may not be aware of just how many factors can affect seal performance. The good news is that every factor can be mitigated to a significant degree, greatly reducing the risk of seal failure.
By fully understanding the importance of installation, the potential for contamination, the amount of friction within the system, the mating surfaces involved, the shaft dynamics and the fluid conditions, designers can select a seal that will function for the maximum time possible. We’ll examine each factor in detail.
Installation
A seal’s lip is key to making sure seal wear is low. The right amount of lubricant under the lip keeps friction/wear low without resulting in a leak. Today’s sophisticated seal lips are designed to do just that, but this functionality adds a degree of complication to installation.
First, seal lips (whether rubber or polytetrafluoroethylene [PTFE]) tend to be fragile.
If the geometry of the seal’s installation is not ideal, the seal lip may be damaged or even turned inside out during installation.